The Process of Aluminum Sand Casting
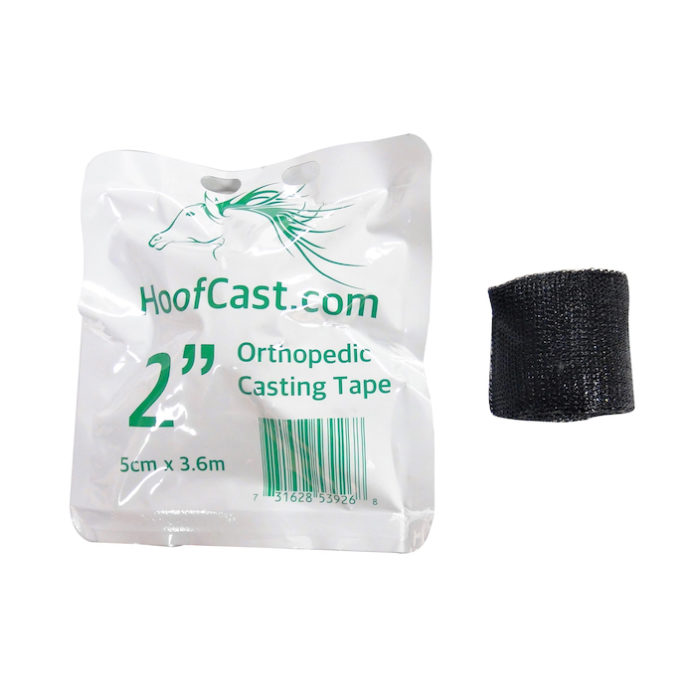
Aluminum Sand Casting is a process of creating a mold in which molten aluminum is poured until it gets solidified. The method is highly efficient, cost-effective, and produces high-quality products. First, a pattern is made of the desired product to be cast. This pattern is then placed in a mold, and a sand mixture is used to create the mold that the pattern will be housed in. The sand mixture must be highly durable and withstand the heat and pressure of molten aluminum, which typically ranges from 680°C to 760°C. Once the mold is complete, the molten aluminum can be poured in, and the sand mold can be removed once it cools.
The Advantages of Aluminum Sand Casting
Aluminum sand casting is an incredibly versatile process due to its ability to produce products with high dimensional accuracy and strength. Additionally, the following are some of the main benefits of Aluminum Sand Casting:
Cost-Effective: Aluminum Sand Casting is a highly cost-effective process because it requires few materials, low set up costs, and the molds can be reused.
Flexible: Aluminum Sand Casting is used to create products in a variety of shapes and sizes with different complexities, all from the same mold.
High Accuracy: Aluminum Sand Casting produces products with high dimensional accuracy, which means that the final product will be a near-perfect replica of the pattern used to create it.
Reduced Waste: The Aluminum Sand Casting process significantly reduces waste. The sand mold can be reused, and the leftover aluminum can be melted down and reused.
The Types of Alloys Used in Aluminum Sand Casting
The choice of alloy for any given Aluminum Sand Casting depends on the required strength, weight, cost, and thermal conductivity of the final product. Below are some of the most commonly used alloys for Aluminum Sand Casting:
Aluminum 355: It is a high-performance alloy that is used for casting engines, cylinder heads, and other high-stress applications.
Aluminum A356: It is a very versatile alloy that is used for a wide range of products in different industries, including automotive parts, marine parts, and aerospace components.
Aluminum 413: This alloy is known for its high strength, thermal conductivity, and ductility. These qualities make it ideal for applications such as electrical connectors, heat exchangers, and other high-stress parts.
Aluminum 319: It is a popular alloy used mainly in industrial products like hand tools, springs, and machine parts.
Conclusion
Aluminum Sand Casting is a highly versatile and reliable technique for producing a wide range of products. With the right combination of alloys, sand mixture, and casting process, this method can yield products with high dimensional accuracy, strength, and durability. It is a process that is not only cost-effective, but also has minimal waste, making it an environmentally friendly option for manufacturers. If you need high-quality, cost-effective, and efficient products, consider Aluminum Sand Casting with the right alloys to meet your manufacturing needs.